The efficiency of computer numerical control (CNC) machining depends on different factors. For instance, it’s highly reliant on the collaboration between the designers and the client, as well as the input from other parties. All the people involved need to deliver what’s expected of them to make CNC machining possible.
Among all the tools available for these tasks, CAD can help people perform these processes in sync for better delivery of CNC machining. If you’re looking to maximize your CNC machining process, you may be wondering how you can best use CAD. Read on to find out why CNC machining needs to integrate CAD:
1. Increases Productivity
Previously, drawings were drawn by hand, slowing down CNC machining. After all, CNC machining depends on these drawings to manufacture products. However, with CAD, designing has been made easier and faster. Designers can now produce several designs within a short period, increasing productivity and efficiency.
2. Reduces Errors And Wastes
CNC machining requires extreme precision when manufacturing products. Reputable companies such as precision machining company Moseys Productions for example, know first-hand how these processes need accuracy, especially when dealing with products for crucial sectors such as healthcare and medicine. When designers make errors in their drawings, the results can be extremely costly. Because the errors are often realized after production, the design team has to start all over again with the designs to rectify the mistakes.
However, with CAD, the design team can identify the errors and solve them before the software makes any prototypes. Therefore, CAD’s accuracy reduces the wastage of material used during revisions.
3. Allows Flexibility In Design
CAD allows designers to observe the whole manufacturing process from the beginning to the end. This way, if the team feels the need to change an aspect of the design, it can do so before the manufacturing process is complete.
4. Increases Quality And Accuracy
CNC machining requires human intervention to produce high-quality goods. The machines have to be monitored and processes observed in case of any issues. However, the accuracy of the CAD software allows the manufacturers to set the process digitally, reducing the need for supervision.
As discussed earlier, using CAD enables the whole team to engage in the manufacturing process. Therefore, the final product is as desired by the client, and individual team members won’t feel the need to doubt or question the quality of the final product.
5. Increases Efficiency
Integrating CAD into the CNC machining process enables storing documents in the cloud and sharing them with the whole team. If the group consists of members in diverse locations, they can still access the files and engage in productive discussions. This way, all the stakeholders are involved in each manufacturing stage, allowing timely changes or discussions.
CAD also allows the team to track the works they do. By storing files in the cloud, the documents can be accessed anytime and be used in repetitive tasks. With these features, there’s no longer any need to redraw a previously made product. The product’s programming code that’s stored in the cloud can easily be retrieved and fed into the CNC machine for manufacturing.
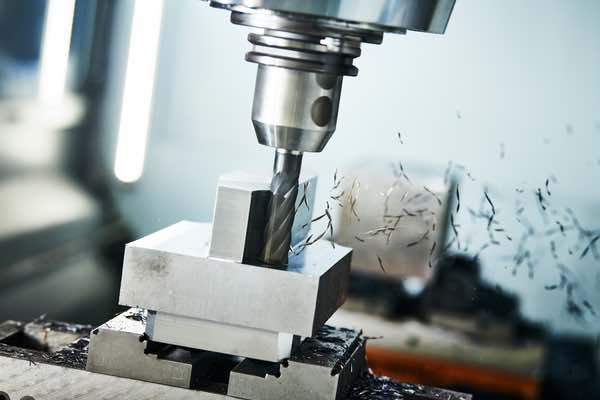
With CAD, the team doesn’t have to experience any delays when waiting for clients to send drawings. Previously, designers drew and redesigned until the ideal product was realized. This consumed much time and reduced productivity in the CNC machining process. CAD helps clients quickly design their desired outcome and send them for the CNC machining to start.
All this increases efficiency in the delivery of the final product to the client’s satisfaction.
6. Grows Your Business
Integrating CAD into CNC machining allows you to take on more complex projects. With the two systems in sync, you can program them to manufacture complex products with minimal or no errors at all. Complex projects are expensive to execute. However, they bring in high returns for CNC machining businesses. This brings in more clients, allowing the businesses to grow.
7. Allows Control Of Projects
Integrating the CAD software into the CNC machining process allows manufacturers to gain total control of their projects. With the manufacturing process being monitored, the design team can make necessary changes as the need arises. By having full control of the project, the final product is as desired from the beginning. The team can also improve the design more easily during this process.
8. Saves Time
CAD reduces errors in the final products. Time is saved since there are fewer revisions on the final product. Fewer revisions mean you can take on the next project as soon as the previous one is done. This increases the turnover of CNC machining and increases returns.
9. Allows Automation Of Processes
CAD does away with the manual drawing and designing of products. This makes the CNC machining process seamless, with no delays and errors in the final product. All these allow you to take on more projects and develop them to perfection with less effort.
Conclusion
As discussed in the article, the advantages of using CAD in CNC machining can be observed in every aspect of the process. CAD might just be what your CNC machining process needs to make it more profitable and fulfilling. The article sheds light on what CNC machining can achieve with CAD.
Now that you know the benefits of integrating CAD into CNC machining, all you have to decide is how soon you can make the necessary changes.
Want to read more about CNC Machining? Here are tips to improve your CAD designs for CNC Machining.